Switchgear maintenance refers to the process of regularly inspecting, servicing, and repairing switchgear, which is the equipment used to control, protect, and isolate electrical equipment in a power system. Its goal is to ensure that switchgear operates efficiently, safely, and reliably.
What Is Switchgear Maintenance?
Switchgear maintenance refers to the process of ensuring that switchgear components are functioning correctly, detecting potential faults, and addressing issues.
This maintenance is vital to the reliable operation of electrical power systems and involves several key aspects:
- Ensuring proper functioning: Switchgear maintenance involves regular checks and servicing to ensure that all parts of the switchgear – such as circuit breakers, switches, and protective relays – are functioning as expected.
This helps maintain the integrity of the electrical system and prevents disruptions in power delivery.
- Detecting and responding to faults: This process involves identifying any faults or potential issues within the switchgear.
By performing regular inspections, testing, and monitoring, maintenance personnel can detect signs of wear, damage, or malfunctions early on.
Quick response to these issues helps prevent system failures and maintain uninterrupted power supply.
- Electrical switchgear maintenance: This includes all activities related to the maintenance of electrical switchgear, including preventive measures, corrective actions, and regular servicing.
This ensures that the switchgear can effectively manage electrical loads and protect the power system from faults.
How Do You Maintain A Switchgear?
Proper maintenance of switchgear is vital to ensuring the safe and efficient operation of electrical systems.
The following are some of the key practices that should be followed when maintaining switchgear:
- Routine inspections
Regular visual inspections are essential to detect signs of wear or damage that could cause equipment failure.
During these inspections, look for signs of corrosion, loose connections, or overheating. Identifying problems early can avoid costly repairs and downtime, ensuring that switchgear remains in optimal condition.
- Testing procedures
Performing regular tests on switchgear is important to verify that it works correctly under a variety of conditions. Common tests include:
- Insulation resistance test: This test measures the insulation resistance of the switchgear to ensure that it can withstand electrical stress and prevent short circuits or equipment failure.
- Circuit breaker testing: This involves testing the tripping mechanisms of circuit breakers to ensure that they operate within the specified time limits, preventing damage to the electrical system in the event of a malfunction.
- Cleaning and lubrication
Keeping switchgear components clean and properly lubricated is important to prevent malfunctions.
Dust, dirt, and moisture can cause corrosion and hinder the performance of moving parts.
Regular cleaning removes contaminants, while lubrication ensures that mechanical parts operate smoothly without excessive wear.
- Documentation
Maintaining a detailed record of all maintenance activities is essential for future reference and compliance with safety standards.
The documentation should include dates of inspections, tests performed, repairs made, and parts replaced.
This helps to track the condition of the switchgear over time and plan future maintenance activities.
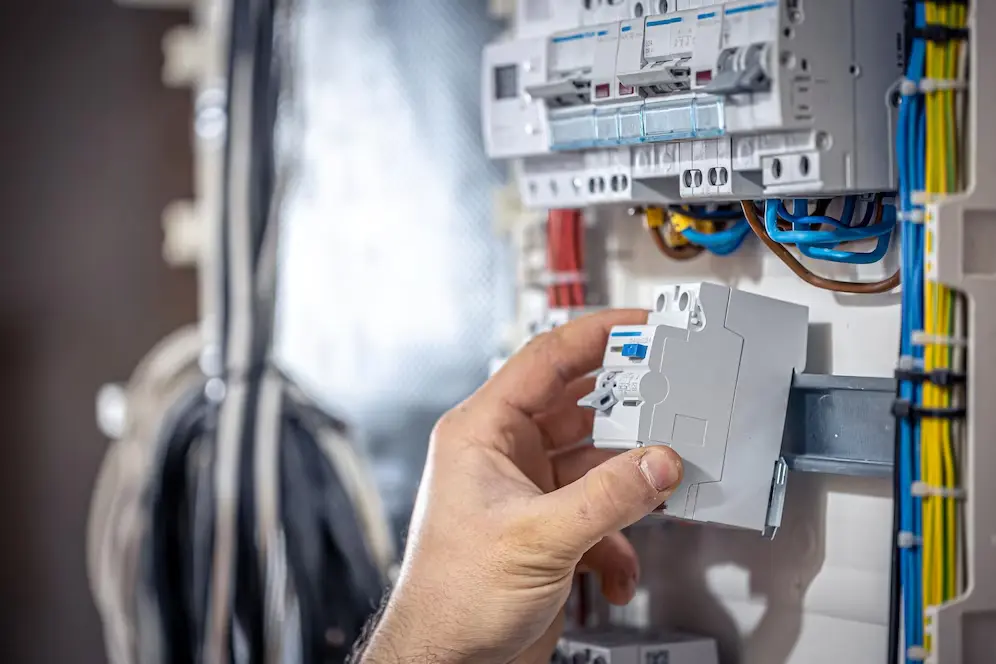
How Often Is Switchgear Maintenance Required?
Switchgear Maintenance schedules can vary depending on some factors, including manufacturer guidelines, the operating environment, and the type of switchgear in use.
Manufacturer Guidelines
Most manufacturers provide specific recommendations about how often switchgear maintenance should be performed.
Generally, electrical switchgear maintenance is recommended every 12 to 36 months.
These intervals are designed to ensure that the equipment remains in optimal condition, reducing the risk of unexpected failures.
Following the manufacturer’s guidelines is essential to maintain the warranty and ensure the longevity of the switchgear.
Operating Environment
The environment in which the switchgear operates plays a significant role in determining how often maintenance should be performed. For example:
- Industrial Environments: In industrial settings, where switchgear is exposed to dust, moisture, and heavy use, more frequent maintenance is necessary.
In such environments high voltage switchgear preventive maintenance may be necessary every 12 months or even more frequently if conditions are particularly severe.
- Residential or commercial environments: In less demanding environments such as residential or light commercial environments, the frequency of maintenance may be increased to 24 or 36 months.
However, even in these environments, it is necessary to perform regular inspections and testing to ensure that the switchgear remains safe and functional.
High voltage switchgear maintenance
When it comes to high-voltage switchgear maintenance, the risks are greater due to the potential consequences of failure.
High-voltage systems are more complex and operate under greater electrical stress, requiring stringent maintenance schedules.
For high-voltage switchgear, preventive maintenance usually involves more detailed inspection, testing, and servicing, often on an annual basis or according to operational demands.
Why Is Switchgear Maintenance Important?
Switchgear maintenance is crucial for the reliable and safe operation of electrical systems. Here is why regular maintenance is necessary:
- Preventing catastrophic failures
Regular maintenance plays a vital role in preventing catastrophic failures that can cause power outages.
Switchgear is responsible for controlling and protecting electrical circuits, and any malfunctions can result in significant disruptions.
By performing regular inspections and testing, potential problems can be identified and addressed before they turn into major problems.
This proactive approach helps avoid sudden breakdowns and ensures a stable power supply.
- Ensuring the safety of personnel and equipment
Proper maintenance is crucial for the safety of both personnel and equipment.
Faulty switchgear can pose serious hazards, including electrical fires, shocks, or explosions.
Regular maintenance, including high voltage switchgear preventive maintenance and electrical switchgear maintenance, helps ensure that all components are working correctly and safely.
This reduces the risk of accidents and increases the overall safety of the work environment.
- Increasing component lifespan
Regular maintenance is crucial to increasing the lifespan of switchgear components.
Regular inspection, cleaning, and lubrication help prevent excessive wear and tear, reducing the likelihood of premature failures.
By addressing minor problems before they become major issues, well-maintained switchgear can operate efficiently for longer, reducing the need for costly replacements and repairs.
- Ensuring a reliable power supply
Well-maintained switchgear ensures a more reliable power supply by reducing the risk of unexpected outages and operational problems.
Consistent maintenance practices such as High Voltage switchgear maintenance contribute to the dependable performance of switchgear, ensuring that the power system remains stable and efficient.
This reliability is essential for uninterrupted operations, especially in critical infrastructure and industrial settings.
- Long-term cost benefits
Investing in regular switchgear maintenance provides long-term cost benefits.
By avoiding unplanned breakdowns and increasing the lifetime of switchgear components, organizations can reduce the frequency and cost of emergency repairs and replacements.
Preventive maintenance helps to effectively manage operating costs, providing better value over time than reactive maintenance approaches.
What Is High Voltage Switchgear Preventive Maintenance?
High voltage switchgear Preventive maintenance involves regular and systematic procedures designed to ensure that high voltage switchgear remains in optimal working condition, reducing the risk of unexpected failures and extending its operational life.
Preventive Maintenance is Important for High Voltage Systems
- Ensuring Safety
High-voltage switchgear operates at significantly higher voltages than standard electrical systems, making it critical to maintain these systems to avoid dangerous electrical faults.
Preventive maintenance helps identify potential problems before they escalate into dangerous conditions, ensuring the safety of personnel and equipment.
- Reducing Downtime
Unexpected failures in high-voltage switchgear can cause significant downtime and operational disruptions.
By performing regular preventive maintenance, problems that could result in system outages can be detected and resolved.
This proactive approach helps keep operations running smoothly and reduces unplanned downtime.
- Increasing equipment lifespan
Regular preventive maintenance, such as cleaning, testing, and lubrication, helps maintain the integrity of high-voltage switchgear components.
This not only prevents premature wear and tear but also increases the overall lifespan of the equipment, leading to long-term cost savings.
- Increasing reliability
High-voltage switchgear systems are critical to the reliable delivery of electrical power. Preventive maintenance ensures that these systems function correctly, increasing their reliability and efficiency.
This reduces the risk of operational failures that can affect power delivery and quality of service.
- Compliance with standards
Preventive maintenance helps ensure that high-voltage switchgear systems comply with industry standards and regulations.
Regular inspection and maintenance activities are often required to meet safety and operational standards to avoid potential legal and regulatory issues.
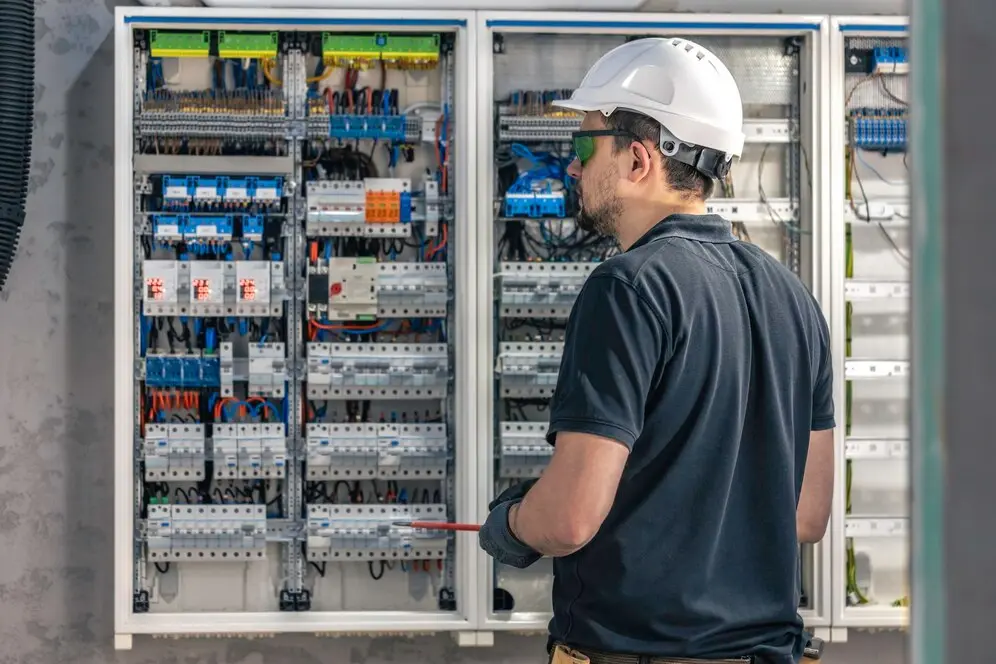
How Is Medium Voltage Switchgear Maintenance Performed?
The maintenance process for medium voltage switchgear involves several preventive steps to address potential problems before they cause significant issues.
Here is a detailed overview of how medium voltage switchgear maintenance is performed:
- Routine Inspection
Preventive maintenance for medium voltage switchgear begins with regular visual inspections. During these inspections, technicians check for signs of wear and tear, such as:
- Corrosion: Inspecting for rust or corrosion on electrical contacts and components.
- Loose Connections: Ensuring that all connections are strong and secure to prevent overheating.
- Physical Damage: Looking for any physical damage to the switchgear housing or internal components.
- Insulation Resistance Test
One of the important tests in electrical switchgear maintenance is the insulation resistance test. This test measures the resistance of the insulation between the conductor and the ground. It helps to:
- Identify insulation degradation: Early detection of insulation degradation can prevent electrical failures and reduce the risk of short circuits.
- Assess the overall condition: Regular testing provides a clear picture of the condition of the insulation and helps to plan necessary maintenance or replacement.
- Circuit breaker testing
Circuit breaker testing is an important part of high-voltage switchgear preventive maintenance. It includes:
- Trip testing: Checking the tripping mechanism of the circuit breaker to ensure that it activates within the specified time during a fault condition.
- Contact resistance testing: Measuring the resistance across circuit breaker contacts to ensure that they are functioning correctly.
- Functional testing: Verifying the overall functionality of the circuit breaker under simulated fault conditions.
- Cleaning and lubrication
Keeping the switchgear clean and properly lubricated is critical to its smooth operation. Preventive maintenance includes:
- Cleaning: Removing dust, dirt, and debris from switchgear components to prevent buildup that can cause overheating or mechanical problems.
- Lubrication: Applying proper lubricants to moving parts to reduce friction and wear, ensuring that mechanisms operate smoothly.
- Thermal imaging
Using thermal imaging cameras to detect hot spots and abnormal temperature variations is another preventive step. This helps identify the following:
- Components overheating: Potential problems that may not show up during routine inspections.
- Potential failures: Areas where temperatures rise may indicate imminent failures or problems that need to be addressed.
- Testing and calibration of protection systems
Regularly testing and calibrating protection systems associated with medium voltage switchgear ensures that they react accurately to fault conditions. This includes:
- Setting verification: Confirm that protection settings are adjusted correctly based on system requirements.
- Response testing: Ensuring that protection devices respond appropriately during fault simulations.
- Documentation and record keeping
Maintaining detailed records of all maintenance activities is important to track the performance and condition of the switchgear. This includes:
- Inspection reports: Documenting the findings from visual inspections and tests.
- Maintenance logs: Recording all cleaning, lubrication, repairs, and replacements performed.
- Performance data: Keeping track of insulation resistance values, breaker test results, and any anomalies observed.
What Is Low Voltage Switchgear Maintenance?
Low voltage switchgear maintenance is critical to ensuring the reliable operation and safety of electrical systems.
It involves a series of activities focused on inspecting, testing, cleaning, and documenting the condition of switchgear components designed to handle voltages up to 1,000 volts.
Effective maintenance helps prevent failures, prolong the life of equipment, and ensure compliance with safety standards.
The Importance of Regular Inspections:
Routine inspections are the cornerstone of low-voltage switchgear maintenance.
This involves systematically checking the switchgear for signs of wear, damage or malfunction.
During these inspections, technicians should look for problems such as:
- Visible damage: Cracks, corrosion, or burnt areas on components.
- Loose connections: Make sure all electrical connections are secure.
- Overheating signs: Detect any signs of overheating that may indicate problems in the switchgear.
The Importance of Cleaning
Another essential aspect of low-voltage switchgear maintenance is cleaning.
Dust, dirt, and debris can accumulate inside switchgear panels and enclosures, leading to:
- Reduced performance: Contaminants can interfere with electrical contacts and components.
- Increased risk of faults: Dirt and dust can cause overheating or short circuits.
Regular cleaning includes removing dust and debris from components and ensuring that vents and cooling systems are unobstructed.
Proper cleaning helps maintain optimal performance and extends the lifespan of switchgear.
Frequently Asked Questions About What Is Switchgear Maintenance
How Frequently Should Switchgear Maintenance Be Performed?
Switchgear maintenance should be performed regularly according to the manufacturer’s recommendations and industry standards.
What Is The Meaning Of Switchgear Maintenance?
Switchgear maintenance refers to the systematic procedures required to keep electrical switchgear in good working condition.