We’ve all been there—installing a new sheet metal only to watch it fail almost immediately. That’s a lug failure in sheet metals (thin plates used in transformers and electronic devices). It is a common issue due to various stress factors that can lead to part damage.
Loosening or failure of lugs in sheet metals can be the reasons. While it can be frustrating, the good news is that many of these failures can be prevented with simple steps. If you are new to the electrical world and wondering what a lug in sheet metal is, then this blog is for you. And if you are an experienced toolmaker looking for solutions, we will clear up all your doubts!
In this guide, we’ll start with the basics of lugs, from their purpose and importance to how to use them. We have also highlighted some common reasons for lug failures and how to prevent them using some easy-to-follow calculations so you can focus more on building and less on fixing.
What Are Lugs In Sheet Metal?
Lugs are connectors that attach cables or wires to various surfaces, such as other cables, terminals, or mechanical structures. Lugs in sheet metal are specifically designed to form strong, reliable connections with metal surfaces, ensuring electrical continuity and structural integrity.
Lugs come in various shapes and sizes depending on their application, and they serve to secure electrical connections, which is essential in industrial and domestic electrical systems.
The design of lugs in sheet metal includes a barrel through which wires or cables pass and a connector end that attaches securely to the sheet metal.
In many cases, these lugs are crimped or soldered to ensure a firm grip, reducing the chance of disconnections, sparking, or mechanical failures.
Flat Lugs In Sheet Metal
A subset of these components is flat lugs in sheet metal, particularly useful for creating streamlined connections.
Flat lugs are favoured for their low-profile design, making them ideal for situations where space and weight are limited, such as in aerospace or compact electrical systems. Flat lugs in sheet metal offer practicality and efficiency by reducing the bulk and weight of the connection, which is why they’re commonly chosen in high-performance applications.
How Do Lugs In Sheet Metal Work?
Their primary function is to transfer current or mechanical force between components. Here’s a breakdown of how lugs work and their applications:
Functionality of Lugs
- Electrical Transmission: Lugs facilitate the transfer of electrical current between a wire and a terminal or between components. For instance, power distribution systems connect cables to transformers or circuit breakers, ensuring minimal power loss. The lug’s conductive material (usually copper or aluminum) ensures efficient electrical transmission.
- Mechanical Force: Lugs also serve mechanical purposes by ensuring a stable connection between different parts, absorbing force without breaking or loosening the connection.
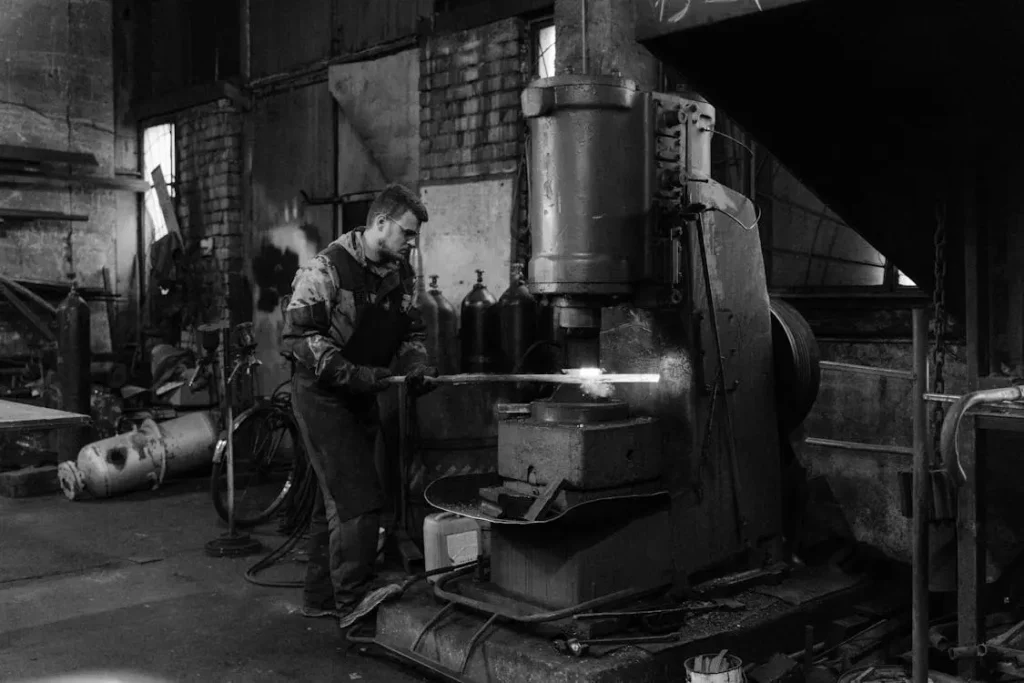
What Are The Purpose And Function Of Lugs In Sheet Metal?
Lugs in sheet metal serve multiple purposes, primarily in electrical and mechanical systems.
Here’s why they’re so important:
- Safety: Improper or loose connections can lead to electrical sparks, fires, or system failures. Lugs help mitigate these risks by providing a stable link between components.
- Structural Integrity: Especially in load-bearing applications, the strength and durability of the connection provided by lugs in sheet metal ensure that the overall structure remains intact under stress.
- Efficiency: Properly installed lugs minimize energy loss, ensuring electrical systems operate at peak performance.
Why Lugs Are Important?
Besides the above reasons, lugs are important connectors for cables and electronic devices. They are important as they:
- Heat Resistance
- Provide Durability
- Reduce maintenance needs
- Ensure Smooth flow of current
- Easy disconnection for testing, diagnosis, and upgrades
- Versatile options to suit diverse applications
Where Are Lugs Used And How Do You Use Them?
Lugs are used across various industries, from automotive and aerospace to construction and telecommunications. Their adaptability to different materials and surfaces makes them a go-to solution for establishing secure connections in diverse applications.
Here are some industries that use lugs in sheet metal:
- Automotive: Used to connect cables and components within vehicles.
- Aerospace: Essential for systems requiring lightweight yet strong electrical connections.
- Construction: Used in building structures for grounding and connecting mechanical parts.
- Telecommunications: Applied in securing cables to terminals in communication systems.
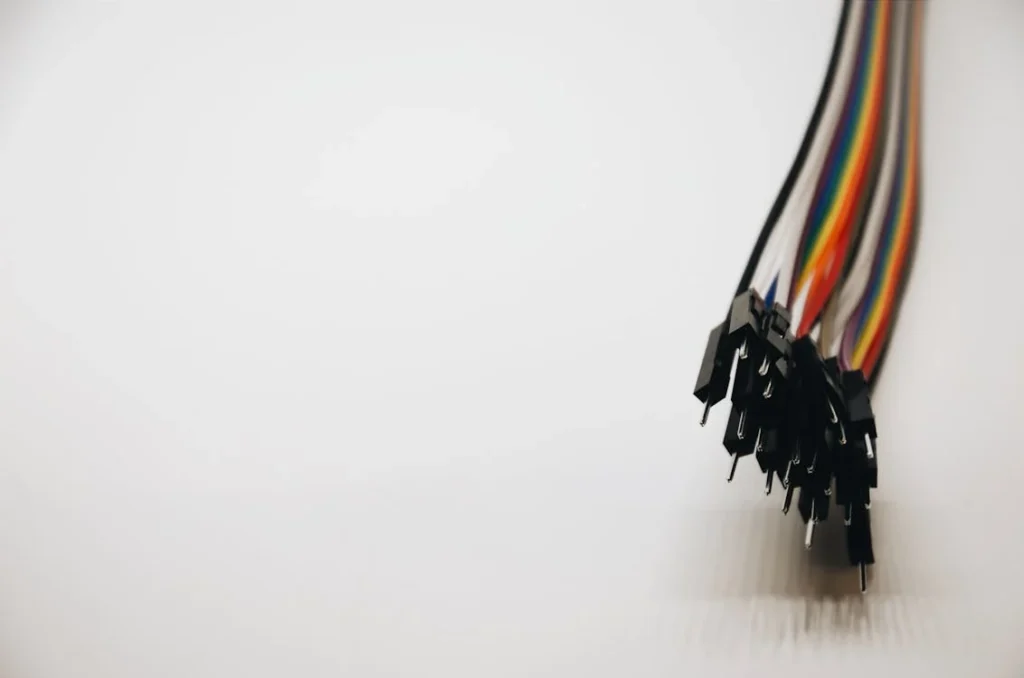
What Are The Different Types Of Lugs?
The following are the different types of Lugs:
- Crimp Lugs: Commonly used for creating secure wire connections by crimping the stripped wire into a barrel, these lugs are used across many industries for their ease of use and reliable connection.
- Compression Lugs: Compression lugs ensure up to 30% more durability than crimp lugs. This is because they are compressed using hydraulic tools. This makes them ideal for high-vibration environments where a more secure and uniform connection is needed, such as in industrial machinery.
- Insulated Lugs: They have an insulating layer that prevents accidental electrical shocks, making them suitable for residential wiring.
- Metal Lugs: Typically made from copper or aluminium, metal lugs are widely used for electrical applications due to their high conductivity. Copper lugs are mostly preferred. Also, studies show that copper lugs have a current-carrying capacity that is 40% higher than some aluminum counterparts.
- Steel Lugs: Steel lugs are ideal for mechanical applications that require durability. They are commonly used in industries where load-bearing connections are critical, such as construction and heavy machinery.
What Is The Size Of A Lug?
Metal sheet lugs come in various sizes. The sizes depend on the type of metal and its intended use. Here are some typical dimensions and factors:
1. Thickness (Gauge) of the Lug
- 14 gauge: 1.897 mm
- 16 gauge: 1.518 mm
- 18 gauge: 1.214 mm
- 20 gauge: 0.914 mm
2. Choosing Lugs Based on Applications
- Heavier gauges (e.g., 12 or 14 gauge) are used for applications needing more durability and strength, such as heavy-duty electrical connectors.
- Thinner gauges (e.g., 18 or 20 gauge) are chosen for lighter applications, like small connectors or mounting brackets.
How To Choose The Right Lug Size?
Besides the above dimensions, below mentioned are some factors to consider when choosing a lug:
- Load Capacity: The lug size should match the load or current it will handle.
- Material Thickness: The quality of the sheet metal will influence the size of the lug required.
- Application: Ensure the lug is designed for the specific electrical or mechanical environment.
Looking for durable lugs? Contact SV Electricals. We are committed to offering high-quality electrical products for 30 years.
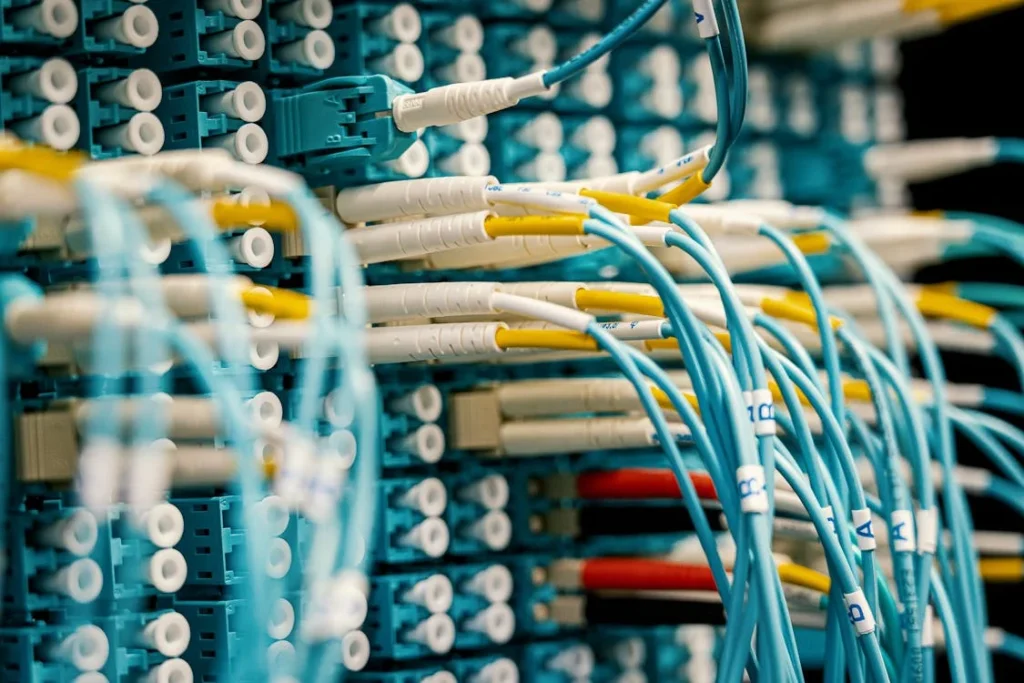
What Are The Common Failures Of Lugs?
If you read till here, you know by now how lug failure is common in sheet metal strips. Here are some common causes of lug failure:
- Poor Installation: If lugs are not crimped or bolted securely, they can come loose, leading to disconnections and system failures.
- Corrosion: Over time, exposure to chemicals or humidity can cause lugs to corrode. This can also be possible due to weather conditions. Corrosion reduces the conductivity and mechanical strength of lugs.
- Overload: Using a lug not rated for the required load or current can lead to overheating, which might cause it to fail.
How To Prevent Lug Failures?
As discussed above, overload or poor installation of lugs on the holes of a part can cause tearing or deformation. These lug failures can be frustrating but do not worry. We have curated some best practices to prevent lug failure in sheet metals:
- Maintain Proper Fastener Spacing: Ensure fasteners are not placed too close to the edges or too close to each other. Use a spacing rule of thumb: the distance from the fastener center to the nearest edge should be at least 1.5x the bolt’s outer diameter.
- Calculate Bearing Strength: To ensure the lugs can handle the load, always double-check your materials’ bearing strength without fail. Always include a factor of safety.
- Do Routine Maintenance: Regularly inspect lugs for signs of wear, corrosion, or loosening.
- Correct Load Rating: Use lugs rated for the load or current they will carry to prevent overheating and damage.
Frequently Asked Questions About Lugs In Sheet Metal
What Are Sheet Metal Lugs?
Sheet Metal lugs are connectors used to connect or terminate cables, wires, power switches, and other electrical appliances.
How Do Lugs In Sheet Metal Work?
Lugs create a secure connection between cables and sheet metal, ensuring electrical continuity and mechanical stability.